DIY CNC Touch probe
I got a little CNC machine a couple years ago and it has been fun to have around. I have cut out all sorts of little things. There is a mount for a Dremmel, a Kite Areal Photography (KAP images) rig, a bunch of wooden gears, some clocks, and other little stuff. Most recently, I have been working on a CNC touch probe. Originally the probe was to help me level the CNC table. It took a little effort and learning but now it is up and running (sort of) and I had to try it out. It is not perfect and there are things I am planning to do to it but I think I have an OK start.A touch probe for a CNC is a pretty simple device. Basically the touch probe is used with the CNC to measure distances of things mounted on the work platform. It mounts on the CNC where the cutter usually is and is moved in one direction, in the Z axis (up and down) for instance, until it touches something and it stops. After it stops it can record the position of the end of the probe to a file. If this procedure is repeated many time you end up with a "point cloud", a map of the hight of the object being measured. The point cloud can be used for many different things. It could be used to create a G-code program to copy the thing that has been measured. It could be used to make a picture or map and I am hoping it can be used to help level my CNC table.
I started out looking at some examples of homemade touch probes. There are a few pretty good ones on the Internet.
http://www.indoor.flyer.co.uk/probe.htm
http://www.brusselsprout.org/CNC/1P-Probe/
http://fadedbits.com/2011/02/touchprobe/
http://www.vinland.com/touch-probe.html
http://www.cnczone.com/forums/digitizing_laser_digitizing/22837-cheap_home_made_touch_probe.html
Expired patent for the Renishaw touch probe.
Google Patents
Some of the sites made things look a little intimidating but I was not looking for super accuracy. This is more of a proof of concept than anything else. So, I got started.
The design
Disclaimer:I am not a super a super engineer or anything. I just threw together the design below to see if I could get anything to work. So, if you try any of this be careful, don't poke out an eye or break anything.
Warning:
The drawings you are about to see are not the prettiest you have ever seen.
Set Up
I am have a Zen Toolworks 7"x7" CNC put together from a kit. It is a little small but has worked out well and been fun.http://www.zentoolworks.com/product_info.php?products_id=74
The stepper motor controller is a Geckodrive G540 4 axis controller. I only have 3 axis but can dream of a forth.
http://www.geckodrive.com/g540-digital-axis-motor-control-p-39.html
As for software to run the CNC I am using EMC2 Ver. 2.4.3. It is free, works well, and runs on Linux. The last item is important as I do not have any computers that run on windows.
http://www.linuxcnc.org/
For a spindle I am using a Bosch Colt router with a 1/4" collet.
To set up the probe I first put put the probe in the router. The shank of the 1/4" bolt is a little small for the collet. Next time I will find something that fits better (I also want a better mount for the router, but that is another story). Please note that with the probe installed in the router it would be a mistake to turn the router on. Spinning at 16,000 RPM, the probe with a 2 foot piece of wire hanging off would, at the very least, make a mess of the project.
Next I hooked up the wires out of the probe to the G540 controller. One goes to pin 1 (corresponds to pin 10 on the parallel port) and the other to ground (pin 12 on the G540)
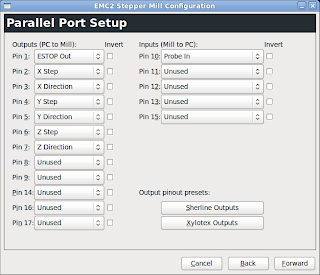
G Code
The sample program that came with EMC2 did not work for me. I don't know why. I did not try to figure it out. I just wrote another little gcode program that probed every position on a grid. It is not fancy but it worked for me.A few notes about the g code.
I set the minimum Z (the deepest I wanted the probe to go) to a little above the table. I did not want the probe to miss something and keep going down.
G38.3 is the code to I used to probe (see the EMC2 users manual). You could also use G38.2. The difference is that G38.3 does not stop for probing errors like reaching the final probe depth and not hitting anything. G38.2 stops the program and reports an error and I did not want this to happen.
I used "G38.3 Z #6" to set the probe to probing. The "G38.3" tells the machine to use the probe. The "Z" tells the machine to probe in the Z direction (you can also probe sideways and other directions, to find the edge of a work piece). The "#6" (where #6 is set at the top of the program to equal 0.05") is as far down as I want the probe to go before stopping.
I added comments in the code, they should help understand the code. I tried to make everything readable but, well, it is not english.
I see not that I forgot to add a line to the top of the g code to tell it to run in inches. I forgot a few things but everything worked ok for me.
; probe.ngc
G94 f2 ; feed inchs/min
; Set up the grid that I want to scan.
; The XY min and max values set up the XY size of the grid
; Set up the grid that I want to scan.
; The XY min and max values set up the XY size of the grid
: The Z min max values define the start of the probing run
; and the end of the run if the probe touches nothing
#1 = 0 ; X min
#2 = 0 ; Y min
#3 = 0.7 ; X max
#4 = 0.6 ; Y max
#5 = 0.12 ; Z max
#6 = 0.05 ; Z min
#7 = 0.01 ; X step
#8 = 0.01 ; Y step
#11 = #1 ; X position
#12 = #2 ; Y position
; move the probe tip up so it does not run into anything
G0 Z #5
; open a file to record the probed results in
(PROBEOPEN probeResults.txt)
O1 Do ; O1 is a loop for X grid values (rows)
#11 = 0 ; set X to 0 at the start of each Y column
O2 Do ; O2 is a loop for the Y grid values (columns)
G0 X #11 Y #12 ; move to new grid position
G38.3 Z #6 ; probe down to the minimum Z value
G0 Z #5 ; raise the probe tip so it does not run into anything
#11 = [#11 + #7] ; add the X step to X, the next grid point.
O2 While [#11 le #3] ; keep this up until reaching the maximum X value
#12 = [#12 + #8] ; done with this row (Xs) move to next column (Ys)
O1 While [#12 le #4] ; keep this up intil reaching the last column (max Y)
(PROBECLOSE) ; close the probe file full of points
G0 Z #5 ; raise the probe tip so it does not run into anything
G0 X #1 Y #2 ; move to the start point
M2 ; end the g code
#2 = 0 ; Y min
#3 = 0.7 ; X max
#4 = 0.6 ; Y max
#5 = 0.12 ; Z max
#6 = 0.05 ; Z min
#7 = 0.01 ; X step
#8 = 0.01 ; Y step
#11 = #1 ; X position
#12 = #2 ; Y position
; move the probe tip up so it does not run into anything
G0 Z #5
; open a file to record the probed results in
(PROBEOPEN probeResults.txt)
O1 Do ; O1 is a loop for X grid values (rows)
#11 = 0 ; set X to 0 at the start of each Y column
O2 Do ; O2 is a loop for the Y grid values (columns)
G0 X #11 Y #12 ; move to new grid position
G38.3 Z #6 ; probe down to the minimum Z value
G0 Z #5 ; raise the probe tip so it does not run into anything
#11 = [#11 + #7] ; add the X step to X, the next grid point.
O2 While [#11 le #3] ; keep this up until reaching the maximum X value
#12 = [#12 + #8] ; done with this row (Xs) move to next column (Ys)
O1 While [#12 le #4] ; keep this up intil reaching the last column (max Y)
(PROBECLOSE) ; close the probe file full of points
G0 Z #5 ; raise the probe tip so it does not run into anything
G0 X #1 Y #2 ; move to the start point
M2 ; end the g code
It turned out a better than I had feared it might and worse than I had hoped. I was not super careful in cutting parts out and putting them together. In fact I was rather cavalier about the whole thing. So, I was happy with what I got and confident I can do better next time.
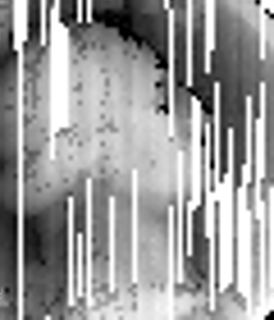
Epilogue
Like I said above, I am happy with the way things turned out. The next one will turn out better. I will be more careful with the construction and I believe that will help with the precision of the device. I also have an idea about how to make sure the switch closes after it is triggered. I think I will use three springs, one above each switch, to push the rod back down instead of the one spring in the center.
I hope this write up is helpful to some one. Let me know what you think. Take care and have a good time.
Gary
Update :(Oct 16, 2012: A while back I made another touch probe. It is much simpler and a description can be found on the blog (here).
Gary,
ReplyDeleteGreat write up. I have been contemplating building a probe for my little CNC machine, but was a little intimidated. You have inspired me. By the way, you made Hack_A_day.
John
John, thanks for the comment. Don't be intimidated by building something like this. It was not to hard. When I do it again though I will take a little more time getting everything straight. I think some of the trouble I am having with the probe skipping is from not having the three rods exactly perpendicular to the probe. Also, I replaced the one spring at the top of the probe with three springs, one above each switch. There are still troubles but it is much better.
DeleteI saw the post on Hack a Day. I like looking over the site every now and then. There are a lot of people doing lots of good things. I had posted a picture of the probe on their Flickr group. Still, I was a little surprised (happily so) to see my pictures of their web site.
I look forward to seeing how you probe goes.
Gary
Hello, You can see my project http://www.cnczucchelli.it Thanks
ReplyDeleteHey there Gary, Jeff from CT Hackerspace. I am wondering if you can get your email address to me.
ReplyDeleteThanks,
Jeff
Wondering how un-level your table is. When I replace the spoilboard on my machine, I use a large (1.25" dia) mortising bit and run it in a spiral pattern over the entire table around .05" deep. This surfaces the table perfectly flat - referenced to the spindle. As long as your spindle is perpendicular to the table you should get a very flat surface. You can use that method to determine if your table surface is far out of level as the bit will miss an area that is lower than that.
ReplyDeleteDave,
ReplyDeleteWhen I wrote this post I know even less about CNC stuff than now and I have learned that the trouble was with the machine in general. The machine (Zen Toolworks 7x7 http://zentoolworks.com/product_info.php?products_id=74) is a little flexible. With a little care everything comes out level but it does take a little care. I do use a spoilboard that I face but sometimes pressing on the table or doing other things the table can get a little out of wack.
By the way, the Zen Toolworks has been great, especially for the price.
Gary
You wired it wrong - if the A is closed, it will not respond to the B or C being opened. So A has to be opened for anything to register.
ReplyDeleteYou should only have two of the small wires, not three.
hello, I used your g-code, and improved.
ReplyDeletehttp://andre-cnc.blogspot.com.br/p/digitalizador-por-contato.html
thank you.
Hello! Gary, the wiring is not correct, say, 2 contacts at port A are connected and 1 or 2 other ports contacts get diconnected, your controller will not see any disconnection. To correctly connect you have to connect wires going to controllers input to contacts from different ports.
ReplyDelete